Awarie maszyn to z pewnością koszmar nie jednego kierownika produkcji. Czy jesteśmy w stanie ograniczyć ilość awarii? Czy operator maszyn jest w stanie wykonać większość czynności związanych z maszyną nie wzywając pracowników utrzymania ruchu? Na te pytania odpowiadamy przedstawiając kolejne narzędzie Lean Manufacturing – TPM.
Czym jest TPM?
TPM (Total Productive Maintenance) czyli kompleksowe, produktywne utrzymanie ruchu, którego głównym hasłem jest „zero nieplanowanych przestojów”. Koncepcja wymyślona w Japonii w latach 60 XX w.
Jest to ciągły proces, który obejmuje wszystkich pracowników poprzez Produktywne Utrzymanie Ruchu prowadzące do optymalnego wykorzystania maszyn. Postęp mierzymy wykorzystując wskaźnik OEE (Overall Equipment Effectiveness), który łączy efektywność pracy, niezawodność maszyn i jakość procesu wytwarzania.
Różnice między tradycyjnym Utrzymaniem Ruchu a TPM
Kluczową różnicą w przedsiębiorstwach wykorzystujących TPM jest zaangażowanie pracowników produkcji do samodzielnej obsługi związanej z konserwacją maszyn. Pozostałe różnice przedstawię w tabeli poniżej:
Tradycyjne Utrzymanie Ruchu | TPM | |
Podejście | Działa – nie ruszaj | Zespołowe usuwanie strat |
Priorytet | Plan produkcyjny | Prewencja |
Działanie | Awarie – gaszenie pożarów | Planowe przeglądy, konserwacja, modyfikacja maszyn, analiza danych, usuwanie źródeł awarii |
Struktura organizacyjna | Osobny wydział UR | UR zintegrowane z produkcją |
Główne cele TPM
– osiągnięcie stabilizacji produkcji poprzez zaplanowane operacje utrzymania ruchu,
– redukcja kosztów przedsiębiorstwa,
– osiągnięcie maksymalnie wysokiej efektywności wykorzystania maszyn w całym okresie użytkowania,
– podnoszenie kwalifikacji pracowników,
– eliminacja strat produkcji, czyli wzrost wskaźnika OEE (całkowitej efektywności maszyn).
Filary TPM
Struktura TPM przedstawiana jest jako świątynia, którego fundamentem jest poprawnie wdrożone 5s oraz wizja trzech zer (zero wypadków, braków, awarii). Filary TPM:
Autonomiczne Utrzymanie Ruchu– polega na zaangażowaniu operatorów do samodzielnej konserwacji, regulacji maszyny. Zwiększa to przede wszystkim świadomość pracowników, a także kompetencje, które pozwalają szybciej wykryć nieprawidłowości.
Planowanie Utrzymanie Ruchu – dzięki drobnym naprawom, regulacjom wykonywanym przez pracowników produkcji dział UR może skupić się na bardziej zaawansowanych pracach, które zostaną odpowiednio zaplanowane.
Wczesne planowanie Utrzymanie Ruchu – w oparciu o nabyte doświadczenie podejmowane są świadome decyzje związane z modernizacją, lub zakupem nowych urządzeń.
Szkolenia – działania związane z podnoszeniem kwalifikacji personelu poprzez realizację planu szkoleń.
Doskonalenie – zgodnie z duchem Lean poszukiwanie nowych, lepszych rozwiązań doskonalących nasz obecny standard.
Zapewnienie jakości – eliminowanie braków poprzez bieżące monitorowanie, rozwiązywanie problemów jakościowych.
Komunikacja – celem jest przede wszystkim poprawa przepływu informacji wewnątrz organizacji.
BHP i środowisko – wszystkie podjęte działania muszą być bezpieczne dla zdrowia pracowników. Dodatkowo należy zatroszczyć się o jak najmniejszy wpływ na środowisko.
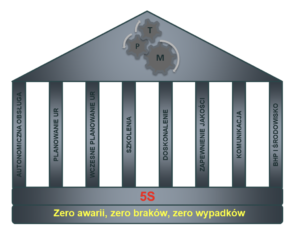
OEE, czyli główny wskaźnik TPM
Wskaźnikiem definiującym postęp Total Productive Maintenance jest OEE (Overall Equipment Effectiveness), którego składową stanowią:
– Dostępność – zależność między czasem zaplanowanym a czasem, który realnie można przeznaczyć (całkowity czas pomniejszony o przezbrojenia, awarie, regulacje, czyszczenia).
– Wydajność – stosunek czasu produktywnego do czasu dostępnego, zaniżany przez straty związane z wykonywanymi operacjami.
– Jakość – stosunek dobrych produktów do wadliwych.
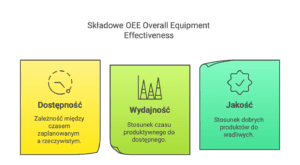
OEE = Dostępność x Wydajność x Jakość
Korzyści wdrożenia
– redukcja kosztów związanych z awariami maszyn
– wzrost wskaźnika OEE
– poprawa jakości
– wykwalifikowany personel
Musimy też oczywiście wspomnieć o nakładzie, jaki niesie za sobą wdrożenie tej aktywności. Najważniejsze aspekty, o których musimy pamiętać podczas podjęcia decyzji odnośnie jego implementacji to:
– świadomość, że fundamentem TPM jest 5S,
– czas (szkolenia pracowników, przygotowanie ustandaryzowanych instrukcji, kart, tablic, zaplanowany czas na konserwacje),
– utworzenie magazynku z częściami zamiennym
Łukasz Powszek