Bezpieczne, ergonomiczne i ustandaryzowane stanowisko pracy to z pewnością miejsce, w którym pracownik jest w stanie wykonywać swoją pracę w sposób najbardziej efektywny.
Jednym z podstawowych narzędzi kojarzonych z Lean Management jest 5s, którego kompletne wdrożenie pozwala utworzyć pożądane środowisko pracy.
Czym jest 5s?
5s jest systemem organizacji miejsca pracy, którego głównym celem jest utworzenie i utrzymanie czystych, bezpiecznych i ergonomicznych miejsc pracy do zapewnienia ciągłości procesów.
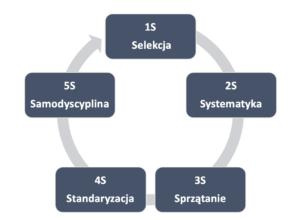
Jest to sposób systematycznego uczenia się dyscypliny, standaryzacji z wykorzystaniem wizualnych narzędzi i dążenia do perfekcji, Składa się z 5 kroków:
1S Selekcja
Pierwszym krokiem jest selekcja, czyli tak naprawdę rentgen stanowiska pracy pod kątem wykorzystywanych narzędzi, materiałów. Należy odpowiedzieć na pytanie, czy dany element wyposażenia, materiał jest nam potrzebny do wykonywania operacji na co dzień. Oczywiście takie pytania zadajemy osobom, które pracują na danym stanowisku. Jest to podstawowa zasada każdego warsztatu optymalizującego😊.
Podstawowa reguła dla tej selekcji to:
Zostawiamy tylko to, co jest potrzebne, w takiej ilości, ile realnie potrzebujemy, wtedy, kiedy potrzebujemy.
2S Systematyka
Zakładając, że pierwszy krok przeszliśmy bez problemów i mamy już narzędzia, które uznaliśmy, że są nam niezbędne, to musimy się zastanowić nad ich optymalnym rozmieszczeniem. Kierujemy się zdrowym rozsądkiem. To czego używamy najczęściej musimy ulokować pod ręką. Wstępnie możemy rozrysować ułożenie i przejść do obserwacji, czy praca operatora wykonywana jest w sposób naturalny. Pytamy i na bieżąco korygujemy.
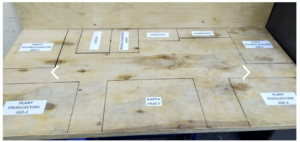
3S Sprzątanie
Mając już za sobą dwa kroki 5S musimy odświeżyć nasze miejsce pracy. Jest to czas, kiedy doprowadzamy nasze stanowisko do perfekcji. Poprawiamy opisy, linie, czyścimy narzędzia, dajemy do naprawy urządzenia, które wymagają naprawy. Jeśli podczas pracy na stanowisku wytwarzamy odpady, to też możemy się zastanowić, czy np. istnieje rozwiązanie.
Pozwoli nam to ograniczać zanieczyszczenia (np. podczas obróbki drewna zastosować urządzenia, które zminimalizują rozprzestrzenianie wiórów). Podczas sprzątania musimy ustalić:
Co, kto, w jaki sposób, czym i kiedy ma czyścić.
4S Standaryzacja
Całą naszą dotychczasową pracę musimy udokumentować w postaci utworzenia jasnych, zrozumiałych dla wszystkich standardów. Jest to czas, żeby przygotować zdjęcia stanu idealnego, harmonogramu czystości, kącików czystości i jeżeli wcześniej nie było to obowiązkiem, to musimy zakomunikować pracownikom, że np. 10 min przed zakończeniem pracy sprzątamy według instrukcji nasze stanowisko pracy.
5S Samodyscyplina
Ostatnim krokiem metodologii 5S jest spięcie wszystkich, poprzednich kroków w całość. Jest to etap, kiedy wraz z zespołem dochodzimy do etapu, żeby wyrobić naturalne nawyki przestrzegania wdrożonych rozwiązań. Jest to z pewnością najtrudniejszy krok, który wymaga zaangażowania najwyższego kierownictwa firmy.
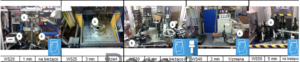
Przy tym puncie warto rozważyć wdrożenie dodatkowej aktywności, która odnosi się do przeprowadzania audytów 5S. Przykładowe pytania jakie możemy tutaj zastosować znajdują się poniżej:
– Czy poprzedni audyt został wykonany?
– Status identyfikacji komponentów znajdujących się na produkcji. Czy jest zachowany?
– Czy operatorzy stosują obuwie i odzież ochronną?
– Odzież ochronna. Czy jest czysta i w dobrym stanie?
– Wskaźniki (np. braki). Czy są prawidłowo i systematycznie wypełniane?
Podobnie jak przy innych wdrożeniach, także tutaj audyt 5S powinien być uruchomiony na obszarze pilotażowym. Dopiero po zwalidowaniu listy pytań powinien być on rozszerzony na pozostałe obszary w przedsiębiorstwie.
Korzyści z wdrożenia 5S
Wdrożenie 5S posiada wiele wymiernych oraz niewymiernych korzyści. Do najważniejszych z nich można zaliczyć:
– poprawa bezpieczeństwa oraz ergonomii pracy,
– obniżenie kosztów przedsiębiorstwa poprzez eliminację marnotrawstwa,
– wypracowany standard podnosi jakość oraz wydajność produkcji,
– redukcja zbędnych rzeczy, materiałów pozwala zaoszczędzić miejsce,
– niewątpliwie czysta hala produkcyjna to godna wizytówka zakładu,
– jest to działanie prewencyjne zapobiegające powstawaniu problemów jakościowych
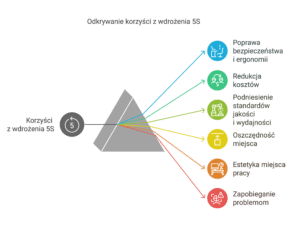
Nakład
Czas i pieniądze przeznaczone na szkolenie załogi, sprzątanie, tworzenie i wdrażanie nowych standardów, zakup potrzebnych narzędzi, środków czystości. W początkowej fazie też warto rozważyć wdrożenie spotkań mających na celu podniesienie świadomości pracowników. Także czynne zaangażowanie kierownictwa jest kluczowe.
5S Podsumowanie
Na pierwszy rzut oka 5s wydaje się bardzo prostym narzędziem. W końcu, co może być trudnego w pozbyciu się zbędnych rzeczy ze stanowiska pracy i ustaleniu nowego standardu. I tu zaczynają się schody, ponieważ często 5s jest krzywdzone i wdrażane w trybie przyspieszonym bez głównych interesariuszy, z pominięciem niektórych kroków.
Często firmy chwalą się systemem 5s, który polegał głównie na zakupie kącików czystości, a tak naprawdę czysto jest w momencie planowanego audytu.
Z pewnością o sukcesie wdrożenia będzie decydował fakt potrzeby wszystkich pracowników do wprowadzenia zmiany, wsparcie najwyższego kierownictwa i powołanego zespołu, który konsekwentnie będzie wprowadzał, monitorował i doskonalił nowe standardy.
Łukasz Powszek pod redakcją Dariusza Kowalczyka