Zarządzanie wyrobem niezgodnym to codzienność w świecie produkcji. Nie unikniesz sytuacji, w której pojawi się defekt, ale możesz nauczyć się nim zarządzać tak, by nie stał się problemem, który uderzy w klienta, reputację firmy albo… zatrzyma całą produkcję.
W tym artykule pokażę Ci konkretne scenariusze i błędy, które wciąż zdarzają się w zakładach produkcyjnych – oraz co zrobić, by ich uniknąć.
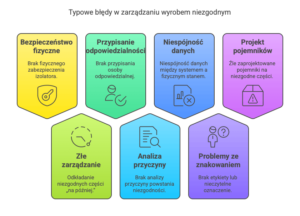
Izolator wyrobów niezgodnych, który nie izoluje – błąd w zarządzaniu wyrobem niezgodnym
W teorii – wyodrębnione miejsce, czerwony pojemnik, opisy, etykiety. W praktyce? Izolator otwarty, brak zadaszenia, a każdy może sięgnąć ręką i wyjąć, co chce. Albo – jeszcze gorzej – całe pomieszczenie lub klatka, która pełni funkcję izolatora, jest stale otwarta. Każdy może wejść, coś włożyć, coś wyjąć. Bez żadnej kontroli.
Tak właśnie wyrób niezgodny wraca na linię produkcyjną, bo ktoś – z niewiedzy albo pośpiechu – sięgnął tam, gdzie nie powinien. Brzmi znajomo? To nie wyjątek, to niestety codzienność w wielu zakładach. Problem polega na tym, że mimo wdrożonej procedury, brakuje realnych barier. A jak nie ma fizycznej przeszkody – to wcześniej czy później ktoś „tylko zerknie” albo „weźmie, bo się przyda”.
Rozwiązanie: izolator to nie ozdoba hali – powinien być zamknięty, fizycznie odseparowany, opisany, a dostęp do niego powinny mieć tylko upoważnione osoby. Jeśli jest to pojemnik – zamykany i z ograniczonym dostępem. Jeśli wydzielona strefa – to taka, do której nie można wejść bez uprawnień. Inaczej to nie zarządzanie wyrobem niezgodnym, tylko pozory porządku.
Złomujesz, ale „najpierw w systemie” – i tu zaczyna się chaos
Końcówka roku. Inwentura. Decyzja: „Złomujemy zalegające komponenty, trzeba zamknąć rok czysto”. Tym razem jednak zaczęto od systemu – części zostały oznaczone jako wyzłomowane. Problem? Fizycznie wciąż były na magazynie. Logistyka, nieświadoma, że to już części niezgodne, kompletowała zlecenie i wysłała je do klienta.
Brzmi jak błąd banalny? A jednak skutki były poważne – produkt z niezgodnym komponentem trafił na rynek i skończyło się reklamacją. Wszystko dlatego, że proces rozpoczęto od systemu, a nie od realnego działania.
Rozwiązanie: najpierw fizyczne złomowanie – usunięcie i zabezpieczenie części. Dopiero potem operacja w systemie: zmiana statusu, rejestracja działań, dokumentacja. To fizyczny stan magazynu powinien być punktem odniesienia – bo to on trafia do klienta, nie systemowe tabelki. Bez zgodności systemu z rzeczywistością nie ma kontroli nad jakością.
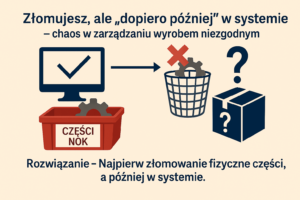
Red Rabbit zjedzony przez system
Red Rabbit, czyli wzorzec negatywny, ma jedno zadanie – testować czujność procesu. Problem pojawia się wtedy gdy przechowywany jest w tym samym miejscu co wyroby niezgodne. Efekt? Ktoś go nie rozpozna, uzna za odpad, wrzuci do złomu – i tyle. W kluczowym momencie nie mamy jak sprawdzić, czy system detekcji działa. A potem zdziwienie, że coś przeszło przez linię.
To typowy przypadek myślenia: „To przecież tylko część – po co tyle zachodu”. Tyle że Red Rabbit to nie jest zwykły komponent – to narzędzie weryfikujące cały proces. Jego zgubienie lub pomylenie z wyrobem niezgodnym może oznaczać, że nie wychwycimy faktycznych błędów.
Rozwiązanie: wzorce negatywne trzymaj osobno, najlepiej w zamkniętym, opisanym pojemniku lub dedykowanym regale. Oznacz je wyraźnie – nie tylko kolorem, ale też dużą etykietą „Red Rabbit – nie usuwać”. Unikniesz w ten sposób wielu niepotrzebnych problemów i nieporozumień.
Izolator braków to nie magazyn
Masz izolator. Masz system. Ale czy masz spójność między jednym a drugim? W wielu zakładach odpowiedź brzmi: „Nie wiemy”. I tu zaczyna się problem. Brak regularnej inwentury izolatora prowadzi do sytuacji, w której dane systemowe nijak mają się do rzeczywistości. W magazynie pusto, a w SAP-ie 12 sztuk. Albo odwrotnie.
A potem przyjeżdża audytor klienta i pyta: „Ile macie fizycznie tych wyrobów niezgodnych?” – a Ty sprawdzasz, liczysz i… zaczynasz się pocić. Bo system pokazuje jedno, a stan faktyczny coś zupełnie innego.
Rozwiązanie: minimum raz w miesiącu rób porównanie: dane z systemu vs. fizyczna liczba sztuk w izolatorze. I to nie tylko dla komponentów, ale i gotowych produktów. To jedyny sposób, żeby naprawdę trzymać rękę na pulsie.
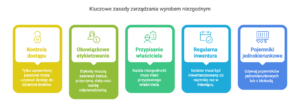
Brak etykiety? Brak pewności w zarządzaniu wyrobem niezgodnym
Czerwony pojemnik, część odłożona z boku, ale… bez etykiety. W teorii wszystko wygląda na zgodne z procedurą. W praktyce? Operator nie wie, co to za komponent – może jest niezgodny, a może ktoś tylko odłożył go „na chwilę”. W takiej sytuacji łatwo o pomyłkę i ponowne wprowadzenie wyrobu niezgodnego na linię.
To nie tylko błąd operacyjny – to ryzyko systemowe. Wystarczy zmiana zmiany, nowy pracownik lub pośpiech w trakcie produkcji, by taka część znowu trafiła do klienta. Bez śladu, bez winnego, bez zabezpieczenia.
Rozwiązanie: każda część trafiająca do izolatora musi być opisana. Etykieta powinna zawierać: status (wyrób niezgodny), datę, przyczynę, osobę odpowiedzialną. To nie fanaberia, tylko elementarny wymóg systemu jakości związanego z identyfikacją.
Brak etykiety to brak decyzji. A brak decyzji to prosta droga do chaosu w zarządzaniu wyrobem niezgodnym.
Inwentura izolatora to nie biurokracja – to Twoje ubezpieczenie w razie kontroli i fundament zaufania do całego procesu zarządzania wyrobem niezgodnym.
Wyrób niezgodny odłożony „na później” – opóźnione decyzje w zarządzaniu wyrobem niezgodnym
Regał przy stanowisku, kilka części odłożonych „na chwilę”, bo ktoś nie miał czasu ich zgłosić. Tyle że ta „chwila” zamienia się w tydzień, potem w miesiąc, aż w końcu nikt nie wie, co to za komponenty. Wyrób niezgodny zamiast w izolatorze – leży gdzieś z boku, bez oznaczenia, bez decyzji, bez odpowiedzialności.
W szczególność ten problem występuje pod koniec zmiany gdy dany komponent nie zostaje odpowiednio opisany, ponieważ lider musiał się spieszyć.
Taki obrazek nie jest rzadkością. W codziennym pośpiechu łatwo usprawiedliwić: „Zajmę się tym później”. Problem w tym, że nikt potem się tym nie zajmuje. A części z „półki rezerwowej” trafiają z powrotem na linię – bo wyglądają jak nowe.
Rozwiązanie: zero wyjątków. Wyrób niezgodny od razu trafia do izolatora. Bez odkładania, bez tymczasowych miejsc, bez czekania na „lepszy moment”. To nie są odpady – to temat wymagający natychmiastowej reakcji.
W zarządzaniu wyrobem niezgodnym nie ma miejsca na odkładanie decyzji. Im szybciej reagujesz, tym większa szansa, że nie skończy się to błędem, reklamacją i stratą wiarygodności.
A kto decyduje, co dalej? – rozmyta odpowiedzialność w zarządzaniu wyrobem niezgodnym
Wyrób niezgodny trafił do izolatora. Świetnie. Ale co dalej? Kto podejmuje decyzję o jego dalszym losie – przeróbka, złom, analiza? W wielu przypadkach… nikt. Bo nikt nie został przypisany. Część czeka tygodniami, aż ktoś w końcu się nią zajmie.
I tak z dnia na dzień temat się rozmywa.
Brak przypisanego właściciela to jak niezamknięty temat w jakości – niby coś zostało zauważone, ale bez dalszego ciągu. Zespół zaczyna się frustrować, bo proces się zacina, a decyzje nie zapadają. A to prowadzi do braku zaufania do całego systemu zarządzania wyrobem niezgodnym.
Rozwiązanie: każda część w izolatorze musi mieć przypisaną osobę odpowiedzialną. Może to być lider zmiany, inżynier jakości czy kierownik działu – ważne, by było wiadomo, kto „trzyma temat”. Najlepiej w systemie lub na karcie wyrobu niezgodnego.
Brak właściciela to brak działania. A brak działania to brak kontroli. W dłuższej perspektywie – chaos.
Brak analizy przyczyny = błąd wraca – utracona szansa w zarządzaniu wyrobem niezgodnym
Złomowanie nie rozwiązuje problemu. Wyrób niezgodny zniknął z magazynu, ale… wróci. Może za tydzień, może za miesiąc – ale wróci, jeśli nie zrozumiemy, skąd się wziął. W wielu firmach analiza kończy się na decyzji „do kosza” – i tyle. Bez 5Why, bez aktualizacji FMEA, bez wpisania do lesson learnt.
Tymczasem każdy wyrób niezgodny to informacja – że coś w procesie nie działa. Jeśli tego nie wykorzystasz, stracisz szansę na poprawę. I co gorsza – pozwolisz, żeby ten sam błąd powtarzał się latami. Cicho, konsekwentnie, kosztownie.
Rozwiązanie: nie zamykaj tematu bez analizy. Ustal przyczynę – nawet jeśli to zajmie chwilę. Skorzystaj z 5Why, sprawdź zgodność z FMEA zarówno procesowego (PFMEA) jaki i logistycznego (LFMEA). Tylko wtedy zarządzanie wyrobem niezgodnym ma sens – jako narzędzie poprawy, a nie tylko sposób na ukrycie problemu.
Zarządzanie bez analizy to jak leczenie bez diagnozy – może pomoże, ale tylko na chwilę. I kosztuje więcej, niż myślisz.
Pojemnik czerwony, ale… możesz z niego też wyciągać niezgodne komponenty
Na pierwszy rzut oka – wszystko wygląda poprawnie. Czerwony pojemnik, odpowiednie oznaczenie, miejsce na linii do odkładania wyrobów niezgodnych. Ale przy bliższym spojrzeniu okazuje się, że otwór wrzutowy jest na tyle duży, że operator bez trudu może sięgnąć ręką i wyjąć część z powrotem. Z ciekawości, przez pomyłkę albo po prostu z wygody.
I właśnie wtedy cały system zaczyna się sypać. Część, która miała być odseparowana, wraca na linię. Bez dodatkowej kontroli, bez decyzji, bez zabezpieczenia. A wszystko przez niedopracowany szczegół, który dodatkowo powinien zostać wykryty podczas projektowania procesu produkcyjnego (PFMEA).
Rozwiązanie: używaj pojemników z zapadką jednokierunkową albo fizycznym ograniczeniem dostępu – tak, by część wrzucona nie mogła zostać łatwo wyjęta. Jeśli coś trafia jako wyrób niezgodny – musi tam zostać, aż do momentu świadomej decyzji.
Zarządzanie wyrobem niezgodnym powinno uwzględniać dbałość o detale. Bo wystarczy jedno „sięgnę z ciekawości”, by uruchomić reakcję łańcuchową, która zakończy się reklamacją od klienta oraz jego potencjalną eskalacją.
Podsumowanie: wyrób niezgodny to nie problem. Brak reakcji to problem – i słabe zarządzanie wyrobem niezgodnym
Nie da się wyeliminować niezgodności w 100%. Ale można zbudować system, który sprawia, że wyrób niezgodny nie wychodzi z zakładu, nie trafia do klienta, nie wraca jako reklamacja.
I właśnie tego uczymy podczas interpretacji wymagań standardu IATF 16949. To też jeden z kluczowych obszarów skutecznego zarządzania wyrobem niezgodnym.
Autor: Dariusz Kowalczyk