Tworząc raport 8D wg. metodologii problem solving dla wewnętrznych lub zewnętrznych problemów jakościowych warto pamiętać o kilku podstawowych zasadach, które sprawią, że będzie on uwzględniał całościowo wszystkie aspekty powstałego problemu pozwalające na wprowadzenie efektywnych działań ze strony organizacji.
Najistotniejsze z nich przedstawiamy poniżej.
Raport 8D, który nie uwzględniania w analizie ryzyka części produkcyjnych przesyłanych do centrum dystrybucji części serwisowych
Opracowując analizę ryzyka należy pamiętać, że oprócz części produkcyjnych, które organizacja wysyła do montowni samochodowych, bardzo często produkowane są także części serwisowe, które są wysyłane do centrów dystrybucji części serwisowych. Przy tej okazji należy pamiętać, że wg. nowej terminologii IATF część serwisowa jest zatwierdzana przez producenta pojazdów (OEM). Część zamienna takiego zatwierdzenia nie posiada.
Dodatkowo niektórzy z klientów (m. in. Stellantis ex-FCA, FORD, GM) posiadają odpowiednią klasyfikację dla reklamacji jakościowych odnoszących się do takich części.

Z tego powodu zawsze musimy odpowiedzieć na dwa pytania, gdy opracowujemy analizę ryzyka w stosunku do części wysyłanych na pierwszy montaż:
- czy wysłano części z takim problemem jakościowym do centrów dystrybucji części serwisowych?
- czy nie należałoby rozszerzyć działań ICA definiowanych w kroku D3 (Interim Corrective Actions) o te obszary: np. wprowadzenie sortownia, wycofanie materiału etc.
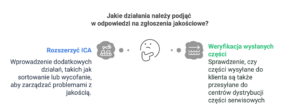
Definiowanie działań w oparciu o symptomy problemu
Takie podejście najczęściej występuje w sytuacji, gdy zespół nie zadał wystarczającej liczby pytań prowadzących do przyczyny źródłowej. To powoduje, że nie rozwiązujemy problemu.
Jest to bardzo krytyczny scenariusz. Dlaczego? Ponieważ może on spowodować dalszą eskalację klienta finalnego. Będzie się to wiązać na przykład z:
- przeprowadzeniem weryfikacji procesu produkcyjnego przez przedstawiciela klienta (SQE, STA)
- lub wprowadzeniem 100% kontroli dla wyprodukowanych części poprzez działania odnoszące się do CSL-1/2 (Control Shipment Level).
Jedyna sytuacja, kiedy organizacja może rozważyć wprowadzenie działań w oparciu o symptomy, dotyczy problemu jakościowego związanego z:
- bezpieczeństwem (Severity 9-10 wg. FMEA)
- lub problemu, odnoszącego się do dużej ilości wysłanych części.
W takim przypadku działania podejmowane są w oparciu o Emergency Response Actions (ERA) definowane w kroku D0 – Identyfikacja problemu.
Brak identyfikowalności podkomponentów oraz wyrobu końcowego
Jeśli nie uwzględnimy kwestii identyfikowalności podczas rozwiązywania problemów 8D, oznacza to, że zajęliśmy się nią za późno. Tego rodzaju podejście powinno być przeanalizowane w pierwszej fazie APQP związanej z planowaniem projektu.
Kluczowym czynnikiem, który należy wziąć pod uwagę przy określaniu właściwej identyfikowalności, będzie ryzyko niezgodności związane z podkomponentami i ich wpływ na produkt końcowy (en. severity).
Więcej informacji dotyczących metodologii, wraz z praktycznymi ćwiczeniami, przedstawianych jest podczas dedykowanych szkoleń. Dodatkowo szkolenie to oferujemy jako nagrania video dostępnych przez 12 miesięcy w ramach 8D Problem Solving.Na stronie Bezpłatne narzędzia można bezpłatnie pobrać automatyczny formularz Excel z możliwością edycji.
Nazwa dokumentu: Raport 8D – formularz Excel
Autor: Dariusz Kowalczyk