Nawet jeśli wdrożyliśmy działania definitywne w kroku D5 nie mamy gwarancji, że problem ponownie nie wystąpi. W tym celu należy opracować odpowiednie działania prewencyjne zapobiegające ponownemu pojawieniu się problemu.
Dokument można pobrać bezpłatnie ze strony z możliwością modyfikacji.
W przypadku zastosowania raportu 8D taką możliwość otrzymujemy w kroku D7.
D7 działania prewencyjne – podstawowe informacje
Definiując strategię w kroku D7, nie możemy zapomnieć o tym, że wdrożone działania korygujące muszą zapobiegać nie tylko ponownemu wystąpieniu tych samych problemów w produkcji danego wyrobu, ale również dotyczyć:
- wszystkich wyrobów gotowych, które wytwarzane są na tych samych lub w podobnych warunkach. W tym wypadku możemy rozważyć gniazdo produkcyjne, proces, materiał, linię produkcyjną lub technologię
- innych wyrobów, które charakteryzują się podobną konstrukcją lub są z tej samej rodziny wyrobów, np. podnośniki szyb o podobnej budowie, ale do innych modeli pojazdów lub do różnych zakładów klienta
- przyszłych projektów, które będą uruchamiane w zakładzie produkcyjnym dostawcy
- luk w systemie, które spowodowały, że dany problem nie został stwierdzony w kolejnym kroku procesu produkcyjnego, a dopiero u klienta. Nie ograniczamy się tutaj tylko do klienta wewnętrznego oraz klienta do którego dostarczamy wyroby na montaż, ale uwzględniamy również zgłoszenia z sieci gwarancyjnej.
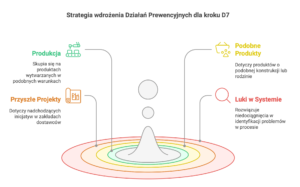
D7 działania prewencyjne – komunikacja podczas wdrożenia
Efektywna komunikacja jest jednym z kluczowych elementów podczas wdrażania zmiany do jakiej oczywiście należy wdrożenie działań prewencyjnych. Dlatego przy tym temacie warto pamiętać o dwóch podstawowych regułach:
- Cały zainteresowany personel musi być poinformowany o wprowadzonych działaniach (w przypadku pracy zmianowej komunikacja powinna objąć wszystkie zmiany)
- Komunikację należy przedstawić na codziennych spotkaniach z kierownictwem, w celu odpowiedniego przypisania zasobów
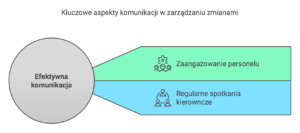
Przykłady działań prewencyjnych
Musimy mieć świadomość, że oprócz częstej praktyki dotyczącej aktualizacji Planu Kontroli oraz PFMEA, mamy dużo innych możliwości odnoszących się do działań prewencyjnych zapobiegających powstawaniu problemu. Należą do nich między innymi aktualizacje dot.:
- wzorców wizualnych
- instrukcji przezbrojenia przeprowadzanych przez pracowników produkcyjnych lub Utrzymania Ruchu
- Flow Chart, czyli diagram przepływu procesu
- LFMEA odnoszący się do obszaru logistyki, jeśli problem był powiązany był z niewłaściwym przemieszczaniem lub składowaniem podkomponentów lub wyrobów gotowych
- informacji przekazanej w ramach bazy Lesson Learned, która będzie uwzględniona przy tworzeniu Flow Chart, DFMEA oraz PFMEA dla nowych projektów – patrz rysunek poniżej
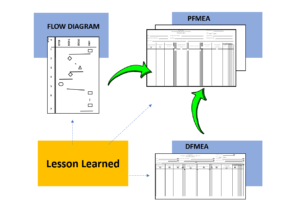
- specyfikacji uwzględniających VoC (Voice of Customer – „głos” klienta) lub (VoP – Voice of Process – „głos procesu”). Ten drugi częściej jest stosowany przy redukcji braków wewnętrznych.
- rysunków – zarówno podkomponentów jak i wyrobów gotowych
- kontroli wejściowej uwzględniającej modyfikację metody pomiaru, częstotliwości oraz dobierania wielkości próbek. W ostatnim przypadku powinniśmy zwrócić uwagę na fakt, że bardziej efektywne jest wybieranie jednej części z każdego gniazda (np. jeśli jest ich osiem), zamiast losowego pomiaru pięciu z nich
- wzorców granicznych (en. boundary samples) lub Katalogu Wad
- instrukcji pakowania wyrobów gotowych
- instrukcji dot. selekcji w przypadku stwierdzenia niezgodności na wyrobie gotowym. Ten scenariusz dotyczy sytuacji, kiedy podczas selekcji i niewłaściwego ponownego pakowania może dojść do uszkodzenia części
D7 działania prewencyjne – a co jeśli nie wdrożymy?
Brak wdrożenia działań prewencyjnych może mieć bardzo poważne konsekwencje dla zakładu produkcyjnego. Jako przykład niech posłuży historia zakładu produkującego metalowe struktury do foteli.
Rozpoczynamy całą historię w chwili przeniesienia tłocznika, który wcześniej był używany do produkcji innego modelu.
Przez pierwsze kilka tygodni produkcja szła sprawnie. Natomiast po pierwszym planowanym przeglądzie przeprowadzanym przez pracowników Utrzymania Ruchu, klient zaczął sygnalizować problem z hałasem oparcia. W trakcie analizy okazało się, że taki sam problem występował we wcześniejszym zakładzie. Wtedy rozwiązano to poprzez dokonanie modyfikacji wysokości jednego z elementów tłocznika.
Natomiast popełniono fundamentalny błąd, nie planując aktywności prewencyjnych dla działań zdefiniowanych w kroku D5. W tym przypadku odnosiło się to do aktualizacji dokumentacji rysunkowej zarówno produkowanego elementu struktury siedzeń jak i dokumentacji dot. danych rysunkowych dla tłocznika.
Na stronie Bezpłatne narzędzia można bezpłatnie pobrać automatyczny formularz Excel z możliwością edycji.
Nazwa dokumentu: Raport 8D – formularz Excel
Serdecznie zapraszam także na udział w szkoleniu 8D Problem Solving w formie nagrań video z 12 miesięcznym dostępem do platformy szkoleniowej.