DVP&R, czyli Design Verification Plan and Report, to narzędzie systematyzujące proces weryfikacji i walidacji produktów w trakcie ich rozwoju. Pełni rolę przewodnika, który pomaga upewnić się, że projekt spełnia zarówno wymagania specyfikacji, jak i oczekiwania klientów.
Dla specjalistów w branży motoryzacyjnej i przemysłowej, którzy codziennie mierzą się z wymaganiami standardów takimi jak IATF 16949, to nie tylko dokument, ale też istotne narzędzie wspierające zarządzanie jakością.
Dlaczego DVP&R jest tak ważne?
Podstawowym celem DVP&R jest uporządkowanie i udokumentowanie procesu weryfikacji projektu. Dzięki temu:
- Możesz monitorować postęp weryfikacji.
- Ułatwiasz współpracę między zespołami projektowymi, inżynieryjnymi i jakościowymi.
- Tworzysz solidną dokumentację, która stanowi punkt odniesienia dla przyszłych iteracji projektu lub nowych produktów.
Kluczowe elementy DVP&R
Każdy dokument składa się z kilku kluczowych sekcji. Oto, co powinien zawierać:
- Funkcje
Opisują, co dany produkt ma robić. Są to podstawowe cele, jakie produkt ma osiągnąć. - Wymagania
To szczegółowe specyfikacje dotyczące jakości, wydajności, czy zgodności z normami lub wymaganiami. - Plany weryfikacji
W tej sekcji opisujemy konkretne testy, analizy lub inspekcje. Dla każdego wymagania powinniśmy mieć jasno określoną metodę testowania. - Raporty weryfikacji
Wyniki testów, w tym ich status (pass/fail, OK/NOK etc), a także wszelkie problemy lub odchylenia od specyfikacji. - Harmonogram
Terminy realizacji testów i analiz, które pomagają efektywnie zarządzać czasem. - Osoby odpowiedzialne
Przypisanie odpowiedzialności za testy oraz dokumentację wyników. - Zasoby potrzebne do weryfikacji
Określenie narzędzi, sprzętu i materiałów potrzebnych do przeprowadzenia testów.
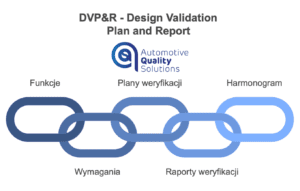
Jak stworzyć skuteczny Design Verification Plan and Report?
Proces tworzenia DVP&R można podzielić na kilka kroków:
- Zdefiniuj cele projektu
Jasno określ, co produkt ma osiągnąć oraz jakie funkcje są kluczowe. - Zidentyfikuj wymagania
Dokumentuj wymagania dotyczące jakości, wydajności i zgodności z normami. - Opracuj plan weryfikacji
Stwórz szczegółowy harmonogram testów i przypisz odpowiedzialność za ich wykonanie. - Przydziel zasoby
Upewnij się, że masz dostęp do odpowiednich narzędzi i sprzętu. - Przeprowadź testy i dokumentuj wyniki
Wyniki powinny być dokładnie opisane, aby wskazać, czy wymagania zostały spełnione. - Przeanalizuj wyniki i dokonaj przeglądu
Zidentyfikuj obszary do poprawy lub dalszego rozwoju.
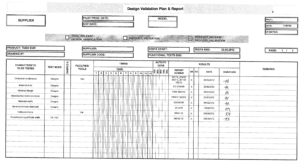
DVP&R a DFMEA – co je łączy?
DVP&R współpracuje z DFMEA (Design Failure Mode and Effects Analysis) w procesie projektowania.
- DFMEA odpowiada za identyfikację potencjalnych ryzyk projektowych i ich skutków („co może pójść nie tak?”).
- Design Verification Plan and Report skupia się na weryfikacji i testowaniu tych ryzyk („jak sprawdzimy, czy działa?”).
Razem te narzędzia tworzą solidną podstawę do zapewnienia jakości w projekcie.
Powiązanie DVP&R z APQP
DVP&R jest kluczowym elementem w APQP (Advanced Product Quality Planning). W ramach wszystkich faz APQP, dokument ten pełni szczególną rolę w weryfikacji i walidacji projektu wspierając procesy dokumentacyjne. Same wyniki testów stanowią natomiast bazę do dalszej optymalizacji. Odbywa się to zazwyczaj w oparciu o Lesson Learned.
Protip!
Jak już wiemy, zespół wykorzystuje powyższy plan i raport w trakcie walidacji nowego projektu. Jeśli bierzesz udział w takim uruchomieniu to warto pamiętać o jednym istotnym elemencie. Jest to czas przechowywania części przeznaczonych testy.
Najlepiej jeśli pokrywałby się on z przedziałem czasowym kiedy będą przeprowadzane testy rekwalifikacyjne. A dlaczego jest to tak istotne?
Dzięki takiemu podejściu możemy udostępnić fizyczne części klientowi. Dzieje się tak w szczególności gry klient sygnalizuje problem z sieci gwarancyjnej, który powinien być wykryty podczas przeprowadzania testów. Jednym z elementów analizy może być też weryfikacja fizyczna części, w celu stwierdzenia czy nie zawierają one dodatkowych pęknięć lub innych defektów, które nie zostały uwzględnione w raporcie.
Pamiętaj – Nie wszystkie testy muszą być przeprowadzane w tym samym czasie
O co dokładnie chodzi? W przypadku komponentów, które są wtryskiwane, termoformowanie lub tłoczone pierwsze testy mogą być przeprowadzone na częściach wyprodukowanych przez producenta form. Następnie po ich przetransferowaniu do zakładu organizacji są przeprowadzane dodatkowe testy gdy dostępny jest status oprzyrządowania – Off Tool Off Process. Na język polski możemy go przeprowadzić jako definitywny proces w definitywnej lokalizacji.
Oczywiście można też powtórzyć część testów. Inżyniering klienta oraz nasz ustalają to na pierwszym spotkaniu.
Pamiętaj o wymaganiach klienta
Niektórzy klienci posiadają własne formatki dla DVP&R. Najlepszym przykładem jest grupa Stellantis. Wymaga ona, aby plan testów był przygotowany w oparciu o procedurę Design Verification Plan And Report (DVP&R) (Stellantis Harmonized), która posiada numer QR.10022.
Podsumowanie
DVP&R to niezbędne narzędzie w arsenale każdego specjalisty ds. jakości, inżyniera czy menedżera projektu w branży motoryzacyjnej. Pozwala usystematyzować proces walidacji oraz minimalizuje ryzyko błędów. Wdrażając go, budujesz solidne podstawy dla jakości produktu oraz skutecznej współpracy między zespołami.
Na stronie Bezpłatne narzędzia można bezpłatnie pobrać formularz Excel – Design Validation Plan & Report (DVP&R). Możesz go oczywiście edytować w dowolny sposób.
Autor: Dariusz Kowalczyk