Design of Experiments (DoE) to zestaw metod statystycznych i inżynieryjnych umożliwiających zaplanowanie, przeprowadzenie i analizę eksperymentów w sposób, który maksymalizuje ilość uzyskanej wiedzy przy minimalnych nakładach testowych.
Dzięki DoE można kompleksowo zbadać wpływ różnych zmiennych na wyniki procesu oraz wyodrębnić kluczowe czynniki wpływające na wydajność systemów inżynieryjnych. Historyczne fundamenty tej metody sięgają prac Ronalda Fishera – pioniera w dziedzinie statystyki, który już na początku XX wieku zaproponował systematyczne podejście do eksperymentowania.
Od tego czasu DoE ewoluowało, włączając nowe techniki i narzędzia, takie jak metody Taguchi czy pełne próby czynnikowe, co sprawia, że dziś stanowi nieocenione wsparcie w optymalizacji procesów produkcyjnych oraz badaniach rozwojowych.
Podstawowe zasady Design of Experiments
W sercu DoE leży wybór odpowiednich zmiennych (czynników) oraz ustalenie dla nich poziomów – zazwyczaj definiuje się dwa poziomy: wysoki (+1) i niski (–1). Takie podejście umożliwia stworzenie pełnych prób czynnikowych (full factorial design), w których badane są wszystkie możliwe kombinacje ustawień czynników.
Dzięki temu inżynier zyskuje możliwość nie tylko oceny wpływu pojedynczych zmiennych, ale także identyfikacji interakcji między nimi. W odróżnieniu od tradycyjnych metod, gdzie testuje się jedną zmienną na raz (one factor at a time – OFAT), DoE pozwala na zbadanie efektów współdziałania czynników.
Metoda jednoczynnikowa często nie ujawnia złożonych zależności, a wyniki mogą być mylące. Dlaczego? Ponieważ ignorują potencjalne interakcje, co czyni podejście DoE znacznie bardziej efektywnym i wiarygodnym.
Metody i techniki stosowane w DoE
Jednym z kluczowych narzędzi wykorzystywanych w DoE są macierze ortogonalne. Są one zaprojektowane tak, aby zapewnić zrównoważony dobór danych – każdy poziom badanej zmiennej pojawia się dokładnie tyle samo razy, co pozwala na niezależną ocenę wpływu poszczególnych czynników.
Techniki te umożliwiają minimalizację aliasingu (konfundowania), czyli sytuacji, gdy wpływy dwóch zmiennych nakładają się na siebie i trudno ocenić ich indywidualny wpływ na wynik. Eksperymenty pełnoczynnikowe (full factorial experiments) polegają na przetestowaniu wszystkich kombinacji ustawień czynników, co w przypadku niewielkiej liczby zmiennych jest praktyczne, jednakże wraz ze wzrostem ich liczby liczba wymaganych testów rośnie wykładniczo.
Dlatego w praktyce często sięga się po alternatywne podejścia, takie jak eksperymenty oparte na metodach Taguchi. Pozwalają zredukować liczbę testów przy jednoczesnym zachowaniu dużej ilości informacji o systemie. Kluczowym elementem jest również technika kodowania zmiennych – poprzez przypisanie wartości –1 i +1 dla odpowiednio niskich i wysokich poziomów, uzyskuje się symetryczny projekt eksperymentu, który ułatwia analizę statystyczną i interpretację wyników.
Analiza interakcji między zmiennymi jest niezwykle istotna. Dzięki odpowiednio zaprojektowanemu eksperymentowi można ocenić, czy zmienne działają niezależnie, czy też ich efekty współdziałają. Na przykład w optymalizacji procesu produkcyjnego parametry takie jak czas, temperatura czy ciśnienie mogą wpływać na wynik pojedynczo.
Jednocześnie mogą też wzajemnie na siebie oddziaływać, powodując nieliniowe zmiany w wydajności. Unikanie aliasingu, czyli mylnego przypisania wpływu jednej zmiennej drugiej, jest więc kluczowe dla uzyskania prawidłowych wniosków.
Praktyczne zastosowania Design of Experiments
DoE znajduje zastosowanie w wielu dziedzinach inżynierii. W sektorze motoryzacyjnym umożliwia optymalizację procesów produkcyjnych, co przekłada się na poprawę jakości produktów oraz redukcję kosztów. Przykładowo, przy optymalizacji parametrów wtrysku tworzywa sztucznego, inżynier może zbadać wpływ zmiennych takich jak:
- prędkość,
- ciśnienie wtrysku,
- temperatura narzędzia,
- czas podtrzymania
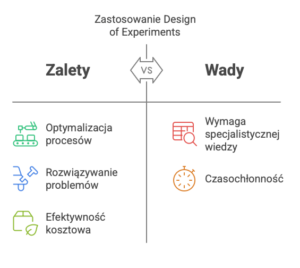
Zastosowanie DoE pozwala ograniczyć liczbę testów (np. do 12 przy eksperymencie pełnoczynnikowym dla wybranych zmiennych). Jednocześnie umożliwia inżynierom identyfikację kluczowych czynników, analizowanie interakcji między nimi oraz tworzenie modeli predykcyjnych.
Dzięki temu można skutecznie wyznaczyć optymalne ustawienia procesu oraz przewidzieć wyniki także dla nieprzetestowanych kombinacji parametrów. Innym przykładem jest wykorzystanie DoE do pozbycia się niepożądanego efektu wizualnego na części dekoracyjnej.
W jednym z projektów związanych z produkcją elementów kabin pojazdów, zauważono niepożądany efekt „skórki pomarańczy” na powierzchniach paneli. Zespół inżynierów, wykorzystując metodologię DoE, zidentyfikował kilka potencjalnych parametrów procesowych – takich jak temperatura nośnika, temperatura prasy, siła docisku, czas laminowania – które mogły wpływać na powstawanie tego defektu.
Dzięki pełnoczynnikowemu podejściu, w którym każdy parametr badano na dwóch poziomach, udało się precyzyjnie określić, które ustawienia miały największy wpływ na redukcję efektu „skórki pomarańczy”. Analiza statystyczna wykazała, że optymalne połączenie parametrów całkowicie eliminowało defekt.
Taki przykład pokazuje, że DoE pozwala szybko zoptymalizować procesy – nawet przy ograniczonych zasobach.
Optymalizacja procesu łączenia elementów
Kolejny, trzeci przypadek dotyczy optymalizacji procesu łączenia elementów, w którym głównym celem było ograniczenie zużycia kleju bez utraty jakości łączenia. W tym projekcie, przy użyciu metodologii DoE, przeanalizowano wpływ pięciu kluczowych parametrów klejarki – takich jak prędkość aplikacji kleju, ciśnienie aplikacji, temperatura, czas nałożenia kleju oraz intensywność mieszania.
Każdy z tych parametrów badany był na dwóch poziomach. Wykorzystując projekt eksperymentu typu full factorial, udało się precyzyjnie określić najbardziej efektywne ustawienia, które pozwoliły zmniejszyć zużycie kleju o 35%, przy jednoczesnym zachowaniu porównywalnej siły oddzielania połączonych elementów, co jest kluczowe dla trwałości i jakości łączenia. Wyniki te przyczyniły się do znaczącej redukcji kosztów materiałowych.
Korzyści wynikające z wdrożenia DoE
Główne zalety stosowania DoE to efektywność oraz oszczędność zasobów. Metoda ta umożliwia pozyskanie pełnej wiedzy o procesie przy minimalnej liczbie testów.
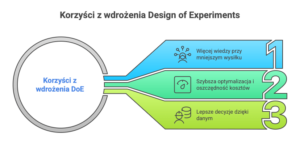
Dzięki temu możliwe jest stworzenie dokładnych modeli predykcyjnych. Pozwalają one przewidywać zachowanie systemu w różnych warunkach, bez konieczności przeprowadzania wszystkich możliwych kombinacji eksperymentów.
Optymalizacja procesów produkcyjnych przy użyciu DoE przekłada się na szybsze wprowadzanie ulepszeń technologicznych, redukcję kosztów oraz zwiększenie konkurencyjności przedsiębiorstwa.
Dodatkowo, wdrożenie DoE pozwala na lepsze zrozumienie złożonych systemów i procesów, co jest niezwykle istotne w branży motoryzacyjnej, gdzie nawet niewielkie usprawnienia mogą przynieść znaczne oszczędności oraz poprawę jakości produktów.
Inżynierowie korzystający z DoE zyskują narzędzie, które umożliwia systematyczną analizę wpływu poszczególnych parametrów na wyniki procesu, co z kolei pozwala na świadome podejmowanie decyzji opartych na solidnych danych.
Podsumowanie i wnioski
Design of Experiments to znacznie więcej niż tylko metoda przeprowadzania testów – to sposób myślenia, który umożliwia dogłębne zrozumienie działania złożonych systemów.
Metodyka DoE umożliwia inżynierom identyfikowanie kluczowych zmiennych, analizowanie interakcji między nimi oraz tworzenie modeli predykcyjnych, które pomagają optymalizować procesy produkcyjne. Wdrożenie tej metody przynosi wymierne korzyści – oszczędność kosztów, większą efektywność badań oraz szybsze wdrażanie ulepszeń technologicznych.
Dla przedsiębiorstw z sektora motoryzacyjnego oraz innych branż, korzystanie z DoE może stanowić przewagę konkurencyjną. Zamiast polegać na metodach prób i błędów, inżynierowie mogą systematycznie badać wpływ wielu czynników jednocześnie, co przekłada się na bardziej precyzyjne i trafne decyzje projektowe.
Autor: Rafał Sobczak