W trakcie fazy uruchomieniowej poprzedzającej SOP (Start of Production) każda organizacja bierze udział w procesie zatwierdzenia części produkcyjnych (en. Production Part Approval Process – PPAP).
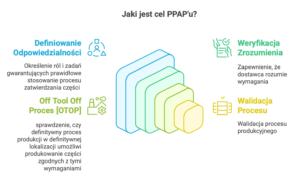
Jest to jeden z etapów zatwierdzenia dostarczanego wyrobu obok zatwierdzenia procesu produkcyjnego oraz walidacji produkowanego wyrobu, która jest nadzorowana przez dział inżynieringu. Celem PPAP’u jest przede wszystkim:
- określenie działań i odpowiedzialności gwarantujących prawidłowe stosowanie procesu zatwierdzania części w fazie uruchomieniowej i produkcji bieżącej
- weryfikacja, czy dostawca rozumie wymagania klienta
- sprawdzenie, czy definitywny proces produkcji w definitywnej lokalizacji (OTOP – off-Tool off Process) umożliwi produkowanie części zgodnych z tymi wymaganiami.
- weryfikacja przejścia w przewidzianym czasie prób przeprowadzanych w celu potwierdzenia,
że definitywny proces produkcji w definitywnej lokalizacji, zachowuje wszelkie charakterystyki funkcjonalne, niezawodnościowe, wymiarowe i estetyczne.
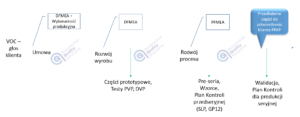
Często można się spotkać też ze sformułowaniem, że PPAP stanowi podsumowanie naszej pracy jako dostawcy i stanowi zwieńczenie zaawansowanego planowania jakości (Advance Product Quality Planning – APQP).
Z punktu widzenia IATF natomiast, wymaganie w skład którego wchodzi PPAP zawarte jest w punkcie 8.3.4.4 – Proces zatwierdzenia wyrobu. Jedną z istotnych rzeczy, o których mowa w tym punkcie jest informacja dotycząca zakończenia procesu zatwierdzania komponentów dostarczanych z zewnątrz (często określanych jako „Buy components”) przed przedłożeniem finalnego wyrobu.
Dodatkowo zaleca się, aby przedłożenie części miało miejsce po weryfikacji procesu produkcyjnego przeprowadzanego wewnętrznie lub zewnętrznie bezpośrednio przez przedstawiciela klienta (SQE, STA ect).
Elementy PPAP
W trakcie procesu zatwierdzenia części produkcyjnych organizacja musi przedłożyć 18 elementów do klienta, które są gwarantem, że dostawca jest w stanie spełnić odpowiednie wymagania jakościowe oraz ilościowe dotyczące produkowanego wyrobu. Należą do nich:
- Zapisy dotyczące wyrobu
- Dokumenty zmian technicznych
- Zatwierdzenie techniczne
- Analiza przyczyn i skutków błędów wyrobu – DFMEA
- Schemat przebiegu procesu
- Analiza przyczyn i skutków błędów procesu – PFMEA
- Plan Kontroli
- Analiza Systemów Pomiarowych – MSA
- Wyniki pomiarów
- Badania funkcjonalne i materiałowe
- Badania zdolności procesów
- Dokumentacja kwalifikowanego laboratorium
- Raport z zatwierdzenia wyglądu zewnętrznego
- Wzorce – części seryjne
- Próbka referencyjna
- Specyficzne wyposażenie do badań i kontroli
- Raport zgodności z wymaganiami specyficznymi klienta
- Potwierdzenie przedłożenia części.
Poziom przedłożenia części (od 1 do 5) wymusza stosowanie dwóch podejść:
- przedłożenie do klienta i zachowanie kopii dokumentów i próbek w odpowiednim miejscu lub
- zachowanie kopii dokumentów i próbek w odpowiednim miejscu i udostępnienie klientowi na życzenie
Jeśli poziom przedłożenia jest nieznany, należy skontaktować się z klientem- domyślnym poziomem jest poziom 3. Dodatkowo zatwierdzenie klienta jest wymagane przed produkcją, odzwierciedlającą maksymalne ilości w odniesieniu do krzywej wzrostu produkcyjnej
Przygotowanie do wyprodukowania części do PPAP’u
Części do zatwierdzenia PPAP muszą być pobrane ze znaczącej partii produkcyjnej (significant production run) tzn. od 1 godziny do 8 godzin i w liczbie minimum 300 kolejnych sztuk. Oczywiście o ile nie ustalono inaczej z klientem na piśmie. Dodatkowo proces produkcyjny powinien być ze statusem OTOP (off-tool off-process).
Oznacza to, że powinien być on definitywny i powinien znajdować się w definitywnej lokalizacji produkcyjnej.
Warto też pamiętać o tym, że przedkładając do klienta części dedykowane pod PPAP powinniśmy spełnić jeszcze jeden warunek. Dotyczy on wcześniejszego uzyskania zatwierdzenia dla wszystkich podkomponentów wchodzących w skład produkowanego wyrobu. Z tego powodu ważna jest komunikacja inżyniera jakości klienta z inżynierem jakości dostawców.
Przykład braku przedłożenia PPAP
Tutaj przede wszystkim musimy być wyczuleni na najbardziej niedocenianą reklamację z powodu dostawy do klienta danego zatwierdzonego seryjnego produktu, który został wyprodukowany na maszynie nie używanej przez 12 miesięcy. W zasadzie jest produkt niezgodny.
Innym często spotykanym scenariuszem jest taki, kiedy dostawca nie informuje klienta o wdrożonej zmianie u poddostawcy. I temat wychodzi podczas reklamacji z sieci gwarancyjnej lub podczas audytu klienta. Należy o tym pamiętać, ponieważ to my ponosimy w oczach naszego klienta odpowiedzialność za naszych dostawców.
PPAP jest również konsekwencją reklamacji. O co dokładnie chodzi? Po reklamacji od klienta jako działanie, czy prewencyjne czy korekcyjne, dochodzi często do znaczącej zmiany w procesie lub w samym produkcie. Wtedy należy wykonać PPAP.
Należy mieć również na uwadze, że PPAP jest dosyć drogą sprawą. Często jest tak, że dla klientów motoryzacyjnych takie PPAP’y są wykonywane za darmo. A w ramach PAPP’u musimy pamiętać o:
- wysyłce części (sampli) przeznaczonych do oceny
- przeprowadzeniu pomiarów na przesłanych częściach
- wykonać badania statystyczne.
Żeby je przeprowadzić, to trzeba zaplanować znaczącą produkcję (en. significant Production). Polega ona na tym, że produkcja odbywa się w sposób ciągły od jednej do ośmiu godzin. Założenie jest takie, że musimy wyprodukować minimum 300 sztuk. Oczywiście musimy uwzględnić tutaj charakter produkcji. Na przykład dla odlewów, które są duże, no takiego podejścia możemy nie stosować.
Jakie są poziomy przedłożenia części do PPAP?
Wyróżniamy 5 poziomów PPAP’u. Są one związane z zawartością dokumentacji. Jeżeli klient nam go nie określił, to domyślnie stosuje się poziom 3. Jest to najbardziej wymagający poziom, w którym trzeba wykonać w zasadzie wszystkie dokumenty z listy 18 przywołanych w podręczniku PPAP AIAG.
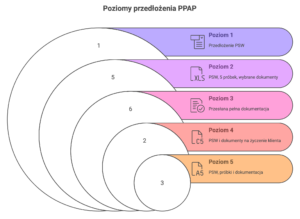
Oczywiście może się zdarzyć, że niektóre nie są dla nas stosowane. Na przykład jeżeli mamy charakterystyki wizualne, które dla naszego produktu nie obowiązują. Pozostałe poziomy to:
Poziom 1
W tym wypadku przesyłamy tylko PSW, czyli. Part Submission Warrant. jest to „najlżejszy” rodzaj PPAP, kiedy klienci mają do nas zaufanie. Mamy długą współpracę, nie mamy problemów jakościowych i faktycznie zmiana nie jest na tyle duża, że nie musimy dostarczyć innych dowodów na to, że produkt nadal będzie zgodny. Od dostawców wymaga on najmniej pracy.
Poziom 2
Przy drugim poziomie też przesyłamy PSW, 5 sztuk próbek i wybrany pakiet dokumentacji, którą sobie wybierze klient. Może to być tylko na przykład wymiarówka dla tych sampli.
Poziom 3
Najbardziej skomplikowany. Tutaj mamy do wysłania wszystkie dokumenty.
Poziom 4
Dla poziomu 4 z kolei przesyłamy PSW i tylko dokumenty, które sobie zażyczy klient. Nie mówimy tutaj teraz o samplach.
Poziom 5
Tutaj mówimy o PSW, sample i pakiet dokumentacji wybranym przez klienta. Natomiast dokumentacja jest do wglądu w lokalizacji dostawcy. Najczęściej przeprowadzany wspólnie z audytem procesu.
Autor: Dariusz Kowalczyk